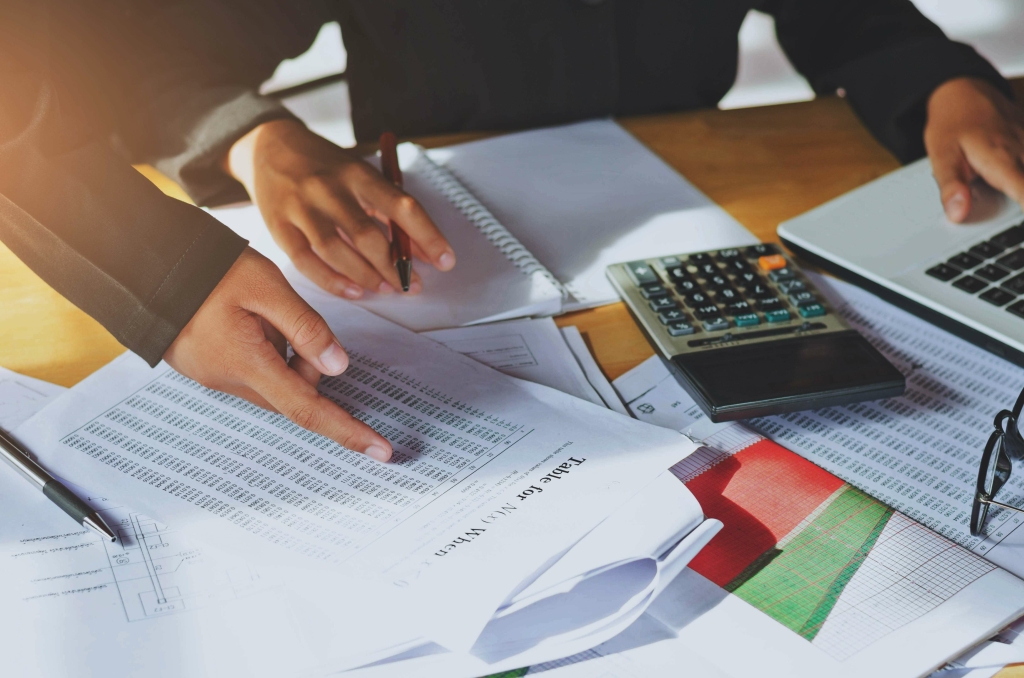
Incremental costs are additional expenses a business spends to expand production. It is the total amount of money paid for producing an additional unit of a product. If no excess capacity is present, additional expenses to consider include investment in new fixed assets, overtime labor costs, and the opportunity cost of lost sales. Like in the above example, it is evident that the per-unit cost of manufacturing the products has decreased from ₹ 20 to ₹ 17.5 after introducing the new product line. Identifying such costs is very important for companies as it helps them decide whether the additional cost is in their best interest.
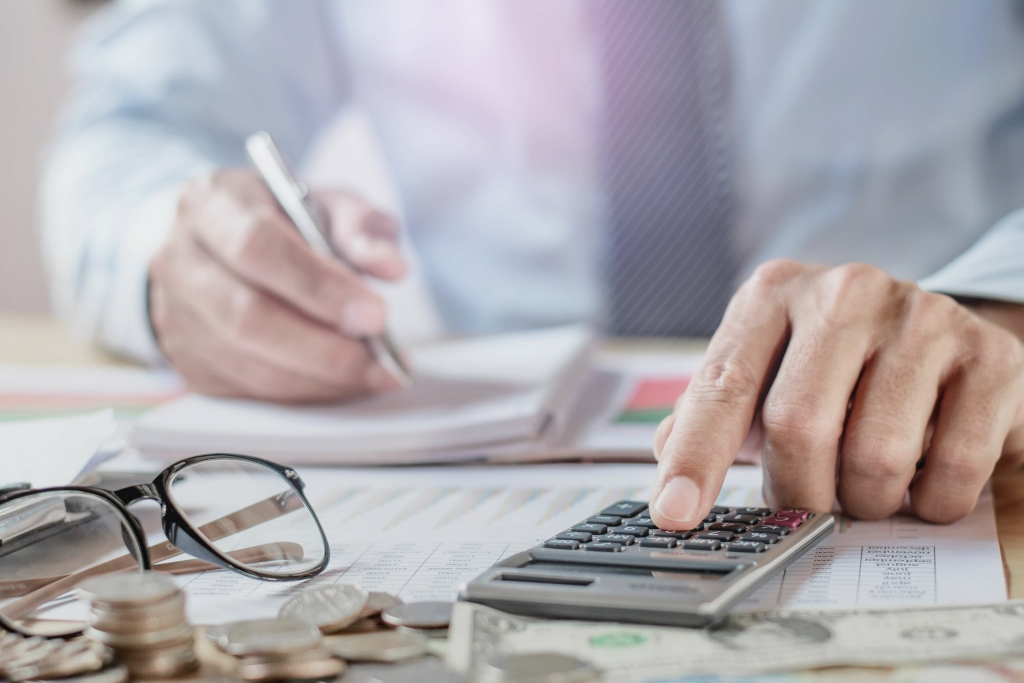
The Value of Calculating Incremental Cost
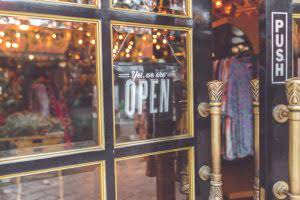
It has lowered as some of your fixed costs have already been covered by your normal production volume. When it comes to managing finances effectively, understanding incremental cost can make a significant difference. Incremental cost, also known as the marginal or differential cost, refers to the additional cost a business incurs when producing or selling an additional unit of a product or service. It is a crucial concept for decision-makers, allowing them to evaluate the profitability of specific actions and make informed choices that contribute to the financial success of their business.
Incremental Cost vs. Incremental Revenue
- Companies seek to maximize production levels and profitability by analyzing the incremental costs of manufacturing.
- Understanding a company’s incremental costs is important for decisions like setting pricing, production levels, make vs. buy, adding product features, and more.
- The cost of producing 15,000 units is $120,000, meaning the additional cost to expand your production to this level is at an incremental cost of $20,000.
- This is makes production-based, decision-making processes more efficient.
- The base case is your existing or normal volume level before any proposed volume increase.
- If a lower price is set for special order, it is vital that the income generated by the special order at least covers the incremental costs.
- They may then determine how much money they can afford to spend on marketing efforts and how much sales volume is required to generate a profit for the company.
Incremental costs are expenses, and producing more units at a particular volume can outweigh the benefits. Here are some incremental cost examples based on different scales of production. The first step in calculating the incremental cost Accounting Periods and Methods is determining how many units you want to add to your normal production capacity. Incremental analysis models include only relevant costs, and typically these costs are broken into variable costs and fixed costs. This shows the incremental cost of scaling monthly production volumes by 5,000 units is $20,000. But if the per-unit cost or average cost is decreasing by incurring the incremental cost, the company might be able to reduce the price of the product and enjoy selling more units.
PERIOD COSTS: Types and Examples
Understanding how to accurately calculate incremental costs is important for making sound business decisions. The overall cost incurred as a result of producing an additional unit of product is referred to as incremental cost. The incremental cost is computed by examining the additional expenses incurred during the manufacturing process, such as raw materials, for each additional unit of output. Understanding incremental costs can assist businesses in increasing production efficiency and profitability. Analyzing production volumes and incremental costs can assist businesses in achieving economies of scale in order to optimize production. Economies of scale occur when expanding production results in cheaper costs because the costs are spread out over a greater number of commodities produced.
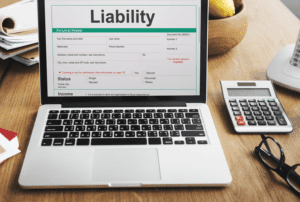
Identifying Relevant Costs
They need to assess the additional development costs (coding, testing, and deployment) against the expected benefits (user engagement, retention, and potential revenue). In summary, while incremental costing provides valuable insights, decision-makers must recognize its limitations. Combining it incremental cost with other decision tools and considering a holistic view ensures better-informed choices. Remember, every decision involves trade-offs, and understanding these limitations enhances our decision-making process.
This analysis enables decision-makers to allocate resources efficiently and optimize their financial outcomes. And there you have it – the five steps to determining incremental costs. While the calculation itself is straightforward, the key is identifying the right base and incremental volumes to analyze. Applying this methodology to your business decisions yields pivotal insights for profitability and strategy. Long-run incremental cost (LRIC) is a cost concept that forecasts expected changes in relevant costs over time. It covers important and significant costs that have a long-term impact on manufacturing costs and product pricing.
- While the calculation itself is straightforward, the key is identifying the right base and incremental volumes to analyze.
- However, care must be exercised as allocation of fixed costs to total cost decreases as additional units are produced.
- This is the increase/decrease in the cost of producing one more additional unit or serving one more additional customer.
- Getting all relevant information about your operational expenses lets you know whether you are in the right financial state to cover additional production costs before starting any project.
- It excludes fixed overhead costs that don’t fluctuate with short-term changes in output.
- It helps businesses identify the additional costs incurred and the corresponding benefits gained by choosing one option over another.
- However, the best pricing policy doesn't cover every possible situation.
- If we look at our above example, the primary user is product 'X' which was already being manufactured at the plant and utilizing the machinery and equipment.
Incremental costs change at different scales of production, and so do their benefits. Businesses must determine the exact volume at which they can get the greatest value. Here the $20,000 incremental cost reveals how much https://www.bookstime.com/ extra the premium feature addition will cost in total across 1,000 product units.
Understanding Incremental Analysis
Furthermore, fixed costs can be difficult to allocate to a certain business area. All of the costs of production are not included to calculate incremental cost. Some of the costs of production are fixed, meaning they do not change when the number of units produced increases or decreases. Incremental cost is how much money it would cost a company to make an additional unit of product.